
How does 3D printing or additive manufacturing work?
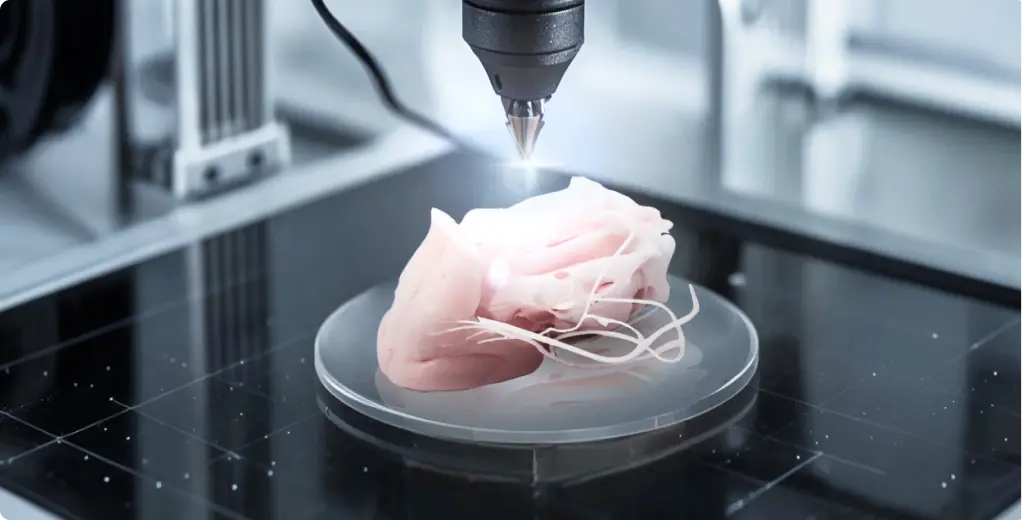
Table of contents
What is 3D Printing?
3D printing, or additive manufacturing, builds objects layer by layer from digital models, creating three-dimensional items with precise customization and efficiency. This approach has unlocked new potential in fields like healthcare, where tailored solutions, such as personalized implants or surgical aids, can now be made on demand.
Overview of Additive Manufacturing Technology
Additive manufacturing, or 3D printing, builds objects layer by layer from digital designs, enabling complex, customized creations that traditional methods can’t achieve. Unlike subtractive manufacturing, which cuts away material, additive manufacturing uses only what’s needed, making it efficient and precise.
In healthcare, this technology allows for the creation of patient-specific models, implants, and devices. Surgeons can use 3D-printed models that match a patient’s unique anatomy to plan and practice procedures, increasing accuracy and reducing surgery time. Patients benefit from custom-fitted prosthetics and implants, enhancing comfort and functionality.
Additive manufacturing is transforming healthcare by making precision and personalization more accessible than ever before.
Why 3D Printing is Revolutionizing Industries
3D printing provides unique advantages like rapid prototyping, reduced material waste, and limitless customization, which are particularly valuable in healthcare. By enabling custom solutions for individual patients, 3D printing is helping clinicians improve outcomes, increase efficiency, and reduce costs.
Core Principles of 3D Printing
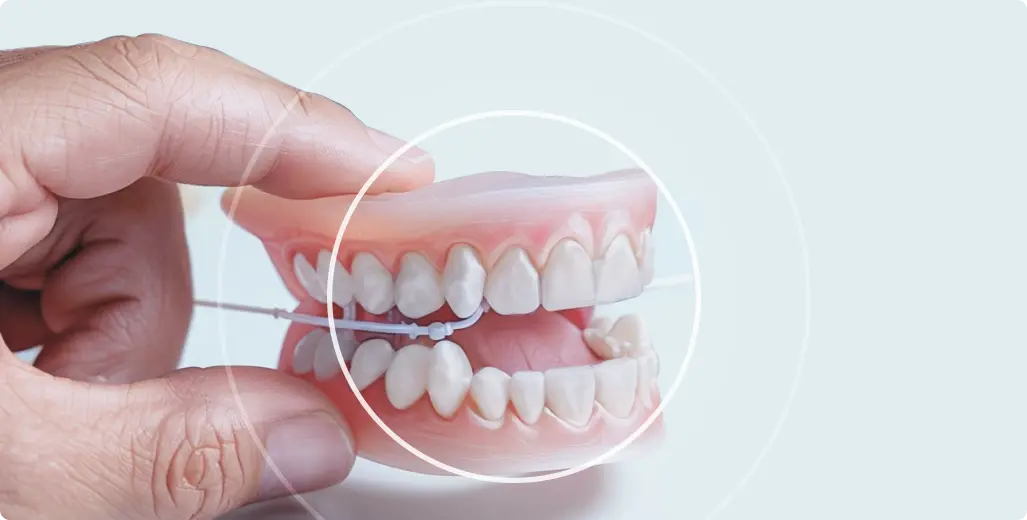
Additive vs. Subtractive Manufacturing
In contrast to subtractive manufacturing, where materials are removed to form objects, additive manufacturing builds up materials layer by layer, creating precise, complex structures. This process is ideal for making custom medical devices that must match a patient’s unique anatomy.
Layer-by-Layer Construction Process
The layer-by-layer approach allows for high accuracy and structural integrity, essential for medical applications like surgical models or custom prosthetics. This precise construction enables healthcare providers to craft detailed models for complex cases, improving planning and patient safety.
The Role of Digital Files and CAD Models
Digital files and CAD (computer-aided design) models guide the 3D printing process, transforming designs into physical objects. In healthcare, these files are critical in creating models that precisely mirror a patient's anatomy, aiding in customized treatments and surgical planning.
Types of 3D Printing Technologies
3D printing has transformed manufacturing across many industries, providing new opportunities for custom, efficient, and innovative production processes. The choice of 3D printing technology depends on factors like the required precision, durability, cost, and application field, especially in industries like healthcare, aerospace, and automotive. Each technology has unique characteristics that suit it for specific uses, from rapid prototyping to highly detailed models for surgical planning. Below are some of the most commonly used 3D printing technologies, along with their key working principles, applications, and advantages.
Materials Used in 3D Printing
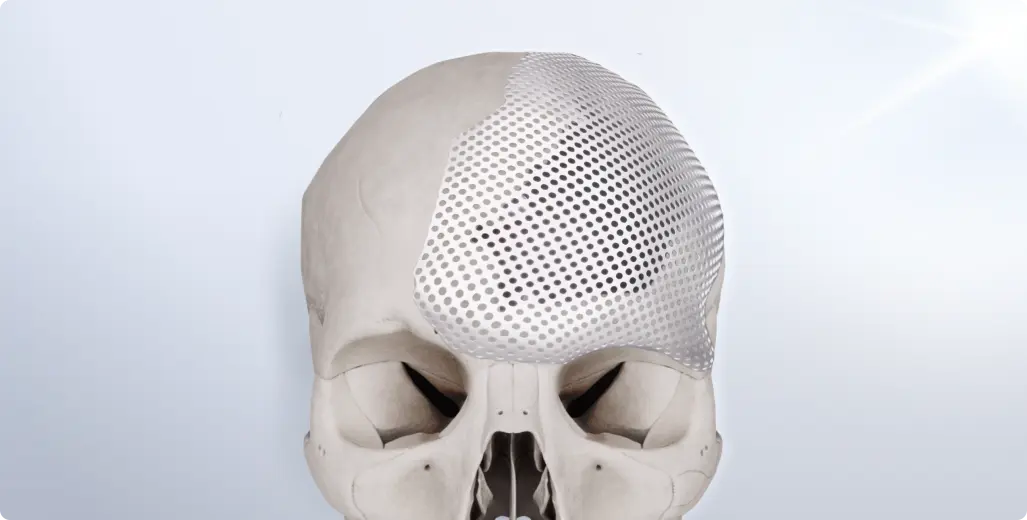
Overview of 3D Printing Materials
3D printing materials vary from thermoplastics to biocompatible metals, each suited to specific applications based on the needed durability, flexibility, and safety.
Thermoplastics
Common in FDM printing, thermoplastics like PLA and ABS are cost-effective and durable, ideal for prototyping and educational models.
Photopolymers
Used in SLA and DLP, photopolymers allow for fine details and smooth finishes, perfect for surgical planning and dental models.
Metals and Metal Alloys
Metals are critical for biocompatible medical implants, offering strength and resilience needed for surgical-grade devices.
Bio-Materials and Specialized Polymers
These materials are used in advanced bioprinting, enabling tissue regeneration and the creation of specialized medical devices.
Considerations for Material Selection
Choosing the right material for 3D printing in healthcare involves balancing factors like biocompatibility, strength, and flexibility, especially for implants and prosthetics that interact closely with the human body. Additionally, cost and ease of sterilization are key, as many medical applications require materials that can withstand frequent cleaning and high temperatures without degradation.
Emerging and Experimental Materials
Innovative materials like bio-inks and biodegradable polymers are expanding the capabilities of 3D printing, particularly in fields like regenerative medicine and temporary medical implants. Meanwhile, cutting-edge materials such as graphene and shape-memory polymers hold future promise for advanced, customizable medical devices that adapt to the patient’s needs.
The 3D Printing Workflow
1. Designing the Model
Creating CAD Files and Choosing Software
Designing begins with digital CAD files, enabling customization based on a patient’s unique anatomy for healthcare applications.
Preparing Files for 3D Printing
File preparation includes ensuring the design is compatible with the 3D printer’s capabilities and settings.
2. Slicing the Model
Understanding Slicing Software
Slicing software translates CAD files into printable layers, detailing layer thickness and other specifications.
Setting Parameters: Layer Thickness, Infill, and Supports
These settings affect the model’s strength and accuracy, which are critical in healthcare models used for surgical planning.
3. Printing the Object
Loading the Printer and Choosing Settings
Once configured, the printer builds the object based on the set parameters, such as material and model requirements.
Monitoring the Printing Process
Close monitoring prevents errors and ensures that the print maintains accuracy, particularly for sensitive medical applications.
4. Post-Processing the Object
Cleaning, Sanding, and Curing Steps
Post-processing can include cleaning and smoothing, which enhances the quality and usability of medical models.
Final Finishing Techniques
Finishing techniques ensure the final model meets high standards for use in healthcare, especially in surgical contexts.
Applications of 3D Printing Across Industries
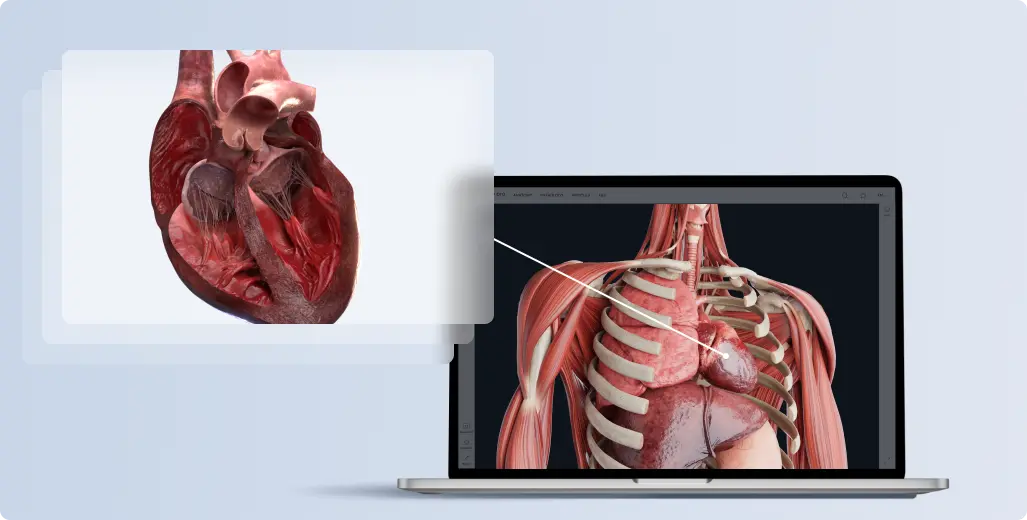
Manufacturing and Automotive
3D printing has become a key tool in the manufacturing and automotive industries by enabling rapid prototyping and efficient tooling, saving time, resources, and costs. Manufacturers can create prototypes quickly, allowing them to test designs, make adjustments, and optimize production far faster than with traditional methods. This agility helps manufacturers stay competitive by accelerating innovation cycles.
Rapid Prototyping and Tooling
3D printing makes it possible to produce prototypes and specialized tools on demand, so manufacturers can quickly assess the feasibility and functionality of new designs. This allows for more experimentation and refinement before committing to large-scale production.
Production of End-Use Parts
3D printing also supports the creation of end-use parts with complex, custom designs. This customization improves both the functionality and cost-efficiency of products, especially in low-volume or specialized runs where traditional methods might be prohibitively expensive.
Healthcare and Medical Innovations
3D printing is transforming healthcare by allowing for the production of custom prosthetics, implants, and patient-specific models that improve treatment precision and outcomes. From creating functional organs through bioprinting to surgical models for pre-operative planning, 3D printing allows for levels of personalization and realism previously impossible.
Prosthetics, Implants, and Bioprinting
With 3D printing, custom prosthetics and implants can be designed to fit each patient’s unique anatomy, improving comfort and performance. Bioprinting, which uses 3D printing techniques to create tissue-like structures, represents an exciting frontier in regenerative medicine, potentially enabling the production of biocompatible tissue or organs.
Patient-Specific Surgical Models
Surgeons use 3D-printed models that match the patient’s anatomy to visualize and plan complex surgeries. 3D modeling and visualization solutions for healthcare enhance this process by creating highly accurate, detailed models that provide surgeons with an interactive view of the anatomy before surgery. These solutions not only increase accuracy but also reduce surgery times and improve patient safety, as they allow surgeons to anticipate challenges before entering the operating room.
VOKA 3D Anatomy & Pathology: Transforming Medical Education with 3D Models
VOKA 3D Anatomy & Pathology provides realistic 3D anatomical models that help medical professionals and students alike visualize both normal and pathological anatomy. This tool supports immersive learning and precise surgical planning, making it possible to practice procedures on life-like models that closely mimic human anatomy. These detailed visualizations elevate medical training and positively impact patient care by better preparing professionals for real cases.
Aerospace and Defense
In aerospace and defense, 3D printing is invaluable for producing lightweight, intricate components that enhance performance and efficiency. By allowing manufacturers to create complex internal geometries, 3D printing reduces weight without sacrificing strength—critical for fuel efficiency and durability in high-performance applications.
Lightweight Parts and Complex Geometries
The ability to produce lightweight, yet durable parts with complex internal structures is essential in aerospace, where every gram matters for fuel efficiency. 3D printing’s precision layering enables intricate designs that are not only strong but also optimized for performance.
Cost-Effective Component Production
3D printing minimizes material waste and enables on-demand production, helping to reduce costs for specialized, low-volume parts that are difficult or expensive to produce with traditional methods. This efficiency is particularly advantageous in prototyping and in meeting the stringent quality standards of aerospace and defense.
Consumer Products and Customization
In consumer goods, 3D printing allows brands to offer highly customized products like jewelry, footwear, and eyewear, meeting individual preferences and driving customer satisfaction. This level of customization aligns with the demand for unique, personalized items and supports sustainable, on-demand production models by reducing inventory waste.
Customized Goods and On-Demand Production
With 3D printing, companies can produce personalized, made-to-order items, reducing excess inventory and providing customers with products tailored to their exact needs. This flexibility also allows businesses to respond quickly to trends or specific customer requests.
Jewelry, Footwear, and More
From intricately designed jewelry to custom-fit shoes and personalized eyewear, 3D printing enables brands to create products that are both visually appealing and comfortable. The result is a unique consumer experience where products are tailored to the user’s specifications, enhancing satisfaction and brand loyalty.
Challenges and Limitations of 3D Printing
Material Limitations and Structural Weaknesses
While 3D printing offers a range of materials, not all are suitable for high-stress or long-term applications, particularly in fields requiring extreme durability, such as aerospace or healthcare. Some materials also lack flexibility, limiting their use in applications that demand elasticity or adaptability.
Print Speed and Scalability Issues
3D printing can be slower than traditional manufacturing methods, especially when producing complex, high-resolution items layer by layer. Scaling up for mass production remains a challenge, as it often requires multiple machines and significant space.
Cost and Accessibility Barriers
High-quality 3D printers and materials can be costly, creating barriers for smaller companies and institutions interested in adopting the technology. Additionally, maintenance and training costs can add to the investment, making it less accessible for low-budget operations.
Quality Control and Consistency
Ensuring consistent quality across multiple prints is challenging, especially when producing highly detailed or functional parts for medical or aerospace applications. Variability in print outcomes can occur due to slight differences in machine settings, material quality, or environmental conditions during the print process.
The Future of 3D Printing and Additive Manufacturing
The future of 3D printing is bright, with advancements in speed, precision, and materials set to broaden its applications in industries like healthcare and aerospace. Faster, more accurate printers are enabling the production of complex, large-scale designs, potentially making 3D printing suitable for high-volume needs.
Emerging materials, such as biocompatible and biodegradable options, are expanding possibilities in healthcare, supporting applications like custom implants and regenerative treatments. Innovations like bio-inks and shape-memory polymers promise breakthroughs in personalized medicine and adaptable medical devices.
With growing adoption across sectors, 3D printing is reshaping manufacturing by enabling on-demand customization and reducing waste. In healthcare, tools like VOKA Anatomy Pro are already revolutionizing medical training, demonstrating 3D printing’s powerful potential to improve patient outcomes and enhance precision in medical procedures.
Conclusion
3D printing is redefining what’s possible in healthcare, delivering custom prosthetics, precise surgical models, and even paving the way for bioprinting—all leading to better patient outcomes and more efficient care. Industries like aerospace and consumer goods are also transformed by 3D printing’s unique ability to reduce costs and create intricate, high-performance designs.
In medical education, innovations like VOKA Anatomy Pro from VOKA demonstrate the power of 3D printing, offering incredibly realistic anatomical models that enhance training and support confident surgical planning. As 3D printing technology advances, it promises a future of greater personalization, efficiency, and sustainability across industries—ushering in a new era in patient care, manufacturing, and beyond.
Table of contents
Thank you for your comment!
Your comment has been submitted for moderation and will be published soon. We'll email you once it’s live.